5 Trending Transportation Updates: December 2016
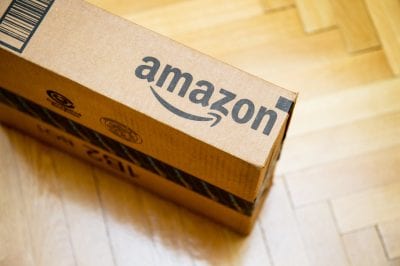
Amazon Innovation: Grocery Stores. Amazon’s first big venture into brick-and-mortal is revolutionary: a grocery store with no cashiers or checkout lines. In the new store, shoppers will scan their Amazon Go app, and the technology will keep track of what you are picking up and add them to your virtual shopping cart. (Read: Omnichannel Takes on Food Industry & Gains Consumer Support)
4 Recommendations to Save Money on LTL Shipments in 2017
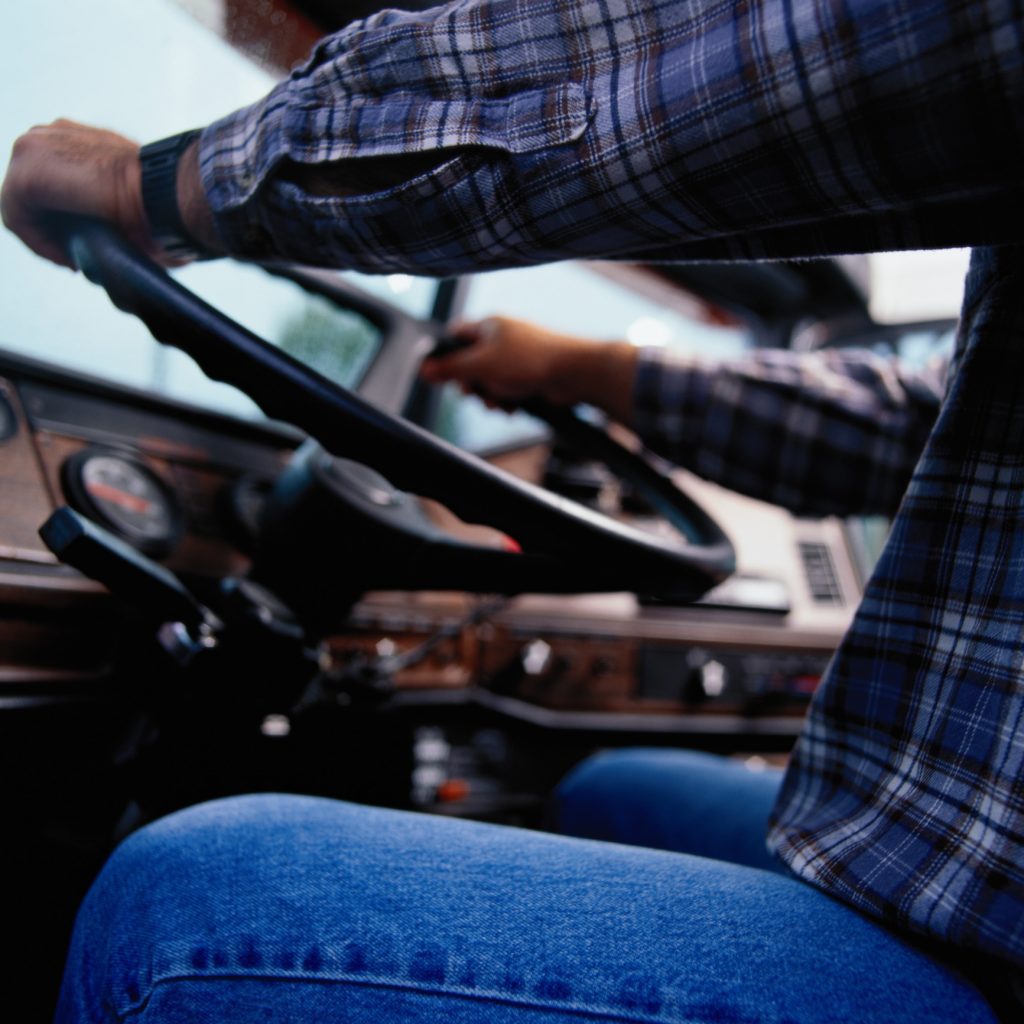
LTL carriers saw all-time high revenues in 2014, then due to a decrease in fuel prices, revenue dropped in 2015. Balanced supply and demand kept LTL prices from dropping in 2016, and JOC.com reports that LTL carriers are looking forward to 2017 as freight volumes are predicted to be higher. Next year, the LTL sector could see a capacity crunch due to the ELD mandate, a slow economy and pricing models. LTL pricing is expected to increase in 2017 and fuel costs aren’t likely to see change. In order to cut LTL freight shipping costs, shippers need to be exact with freight’s weight and dimensions, package and pallet the freight properly, consider consolidation, and utilize transportation management systems.
PLS’ 11 Most Popular Blog Posts from 2016
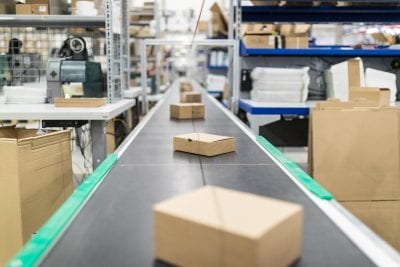
(#11 Most Read in 2016) Seasonal Freight Surge and Consumer Forecast -Fuel prices, weather, capacity, and e-commerce are a few factors that determine truckload demand during the holiday season. Before Thanksgiving, reefer volumes increased and as December’s holiday shoppers start buying, more dry van loads were posted. UPS is expected Monday, December 19 to be the busiest shipping day, and for this year to have 14% more shipping volume than last year. (See the NRF predictions here.)
The Top 6 Supply Chain and Logistics Trends to Watch in 2017
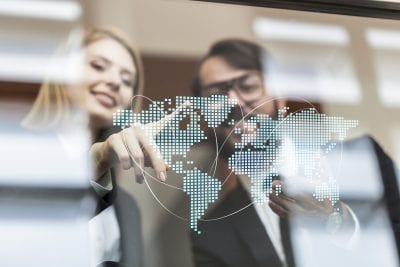
What Are the Top Supply Chain and Logistics Trends in 2017?
Globalization logistics trends 2017
The supply chain is affected by the globalization of business, and those who work with international suppliers don’t have the same competitive advantage they once had. More markets are emerging in the global economy, and traditional supply and demand are changing. Industry Week reports that by 2025, global companies will have procurement managers based in China to source materials and services not only for their operations in that country but for their entire organization. Brazil, Russia, and India are predicted to become sources of supply and demand for global companies. Companies will have to be transparent in supply chain expansion strategies and offer suppliers visibility.
Research Shows Freight Rates Have Gone up in December for 3 Years
The first week of December 2016 had the highest week of volumes on the spot market in the past 2 years. DAT reports that the increase in available loads is because of e-commerce shopping. Denver and Memphis, in particular, saw load availability soar because those markets are distribution hubs for e-commerce.
Same-Day Delivery: 3 Logistics Questions Shippers Need to Answer
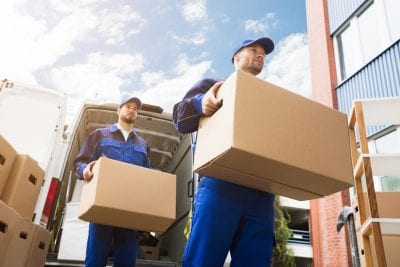
Who is the Same-Day Delivery Consumer?
Consumer expectations are growing. Why? Since companies have tested the same-day delivery option, consumers expect it as the standard. Coldwell Banker says about 53% of US customers are more likely to make an online purchase if they are offered same-day delivery.
What Your Inventory Reveals about Your Reverse Logistics
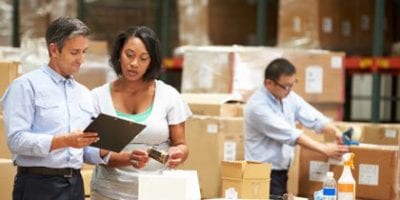
Supply chains share common goals: increase productivity, reduce costs, mitigate risks. Common goals for reverse logistics are to improve customer satisfaction, cut costs, maximize return on assets. Reversing the supply chain means taking in returns, recalls, damaged goods and overstocked merchandise and recapturing its value or disposing of it. With the popularity of online shopping, the supply chain has become more multifaceted, increasing the importance of an organization’s reverse logistics strategy and inventory management practices.
7 Facts about Hazardous Freight Shipping
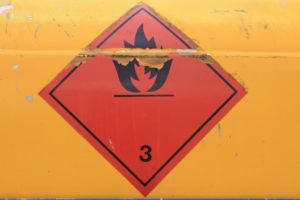
Hazardous materials are substances that the Department of Transportation (DOT) has determined are capable of posing an unreasonable risk to health, safety or property when transported.
Disruption from Your Supply Chain: Product Recalls
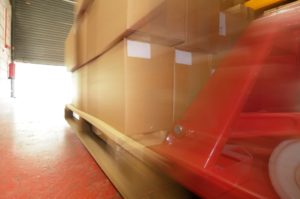
A product recall is a process of retrieving and replacing defective or unsafe consumer goods. When a company issues a recall, the company or manufacturer absorbs the cost of replacing and fixing those defective or unsafe products. Recalls create tension in the supply chain and test consumer relationships, affect sales, and can negatively affect a brand’s reputation.
PLS Logistics Services Releases Mobile Apps for Shippers, Dispatchers, Carriers
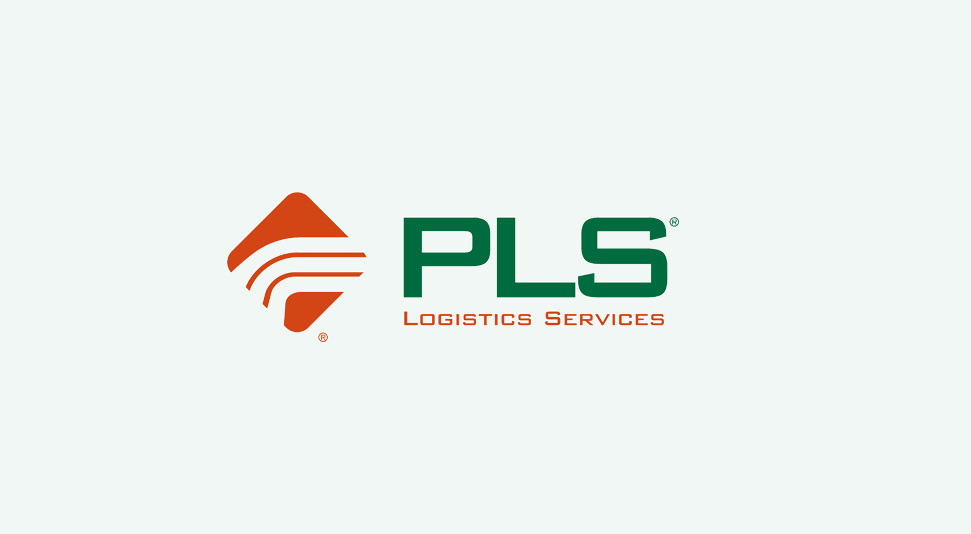
PLS Logistics Services (PLS), a leading provider of technology-enabled transportation management and freight brokerage services, announced today it has released two mobile applications: PLS Live Track and PLS Carrier Connect. Live Track is used by client-shippers and Carrier Connect is used by dispatchers and drivers.