September Transportation News Recap
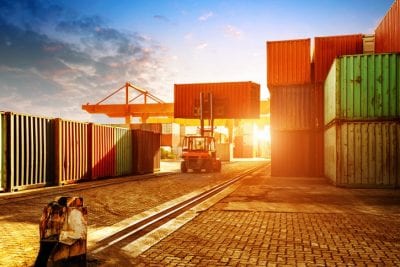
Here is a quick summary of some of the most talked about transportation, supply chain and logistics topics from September 2015:
PLS Logistics Services Named One of Pittsburgh’s Coolest Office Spaces
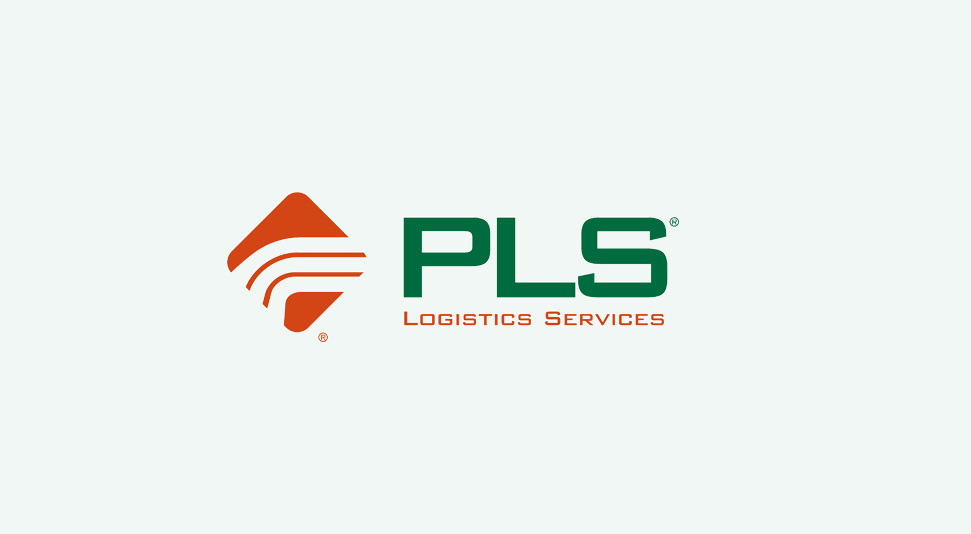
PLS Logistics Services (“PLS”), a leading provider of technology enabled transportation management and freight brokerage services, was recognized as one of Pittsburgh’s coolest offices by the Pittsburgh Business Times.
Do I Need Logistics Management for Mining, Oil & Gas Operations?
Logistics management for oil and gas industry
The mining, oil, and gas industries have the most complex supply chain challenges. Exploration tends to be in remote locations with no transportation infrastructure, and typically requires bulk equipment and extensive safety policy. Any shipping disruption results in a significant loss for an industrial company.
The Best Way to Drive Consistency in Freight Transportation

The supply chain is always moving and prone to disruptions, which can make consistent delivery difficult. You want customers to trust that you’ll meet their expectations, but disruptions are often out of a company’s control. Your customer won’t care what the problem is; they will only view delays as poor service.
Highlighting Change for Truckers #NTDAW
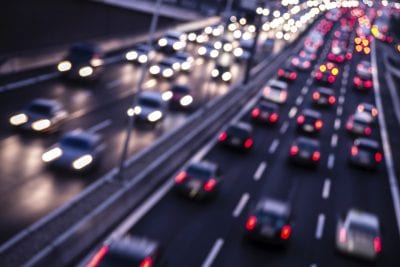
New technological advancements, changes in regulations and shifting shipping trends have made the transportation industry an exciting, and often challenging, environment to work in. Truck drivers especially are noticing new trends in the industry – from same-day delivery expectations to automated vehicles and a proposal to lower the age minimum of drivers.
What’s Happening with Hours of Service (HOS) Rules?
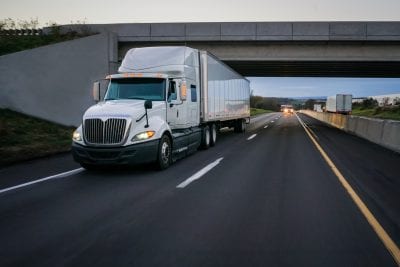
In July 2013, the Federal Motor Carrier Safety Administration (FMCSA) implemented some significant changes to the way drivers record their hours on duty. The 3 main changes included were:
National Truck Driver Appreciation Week
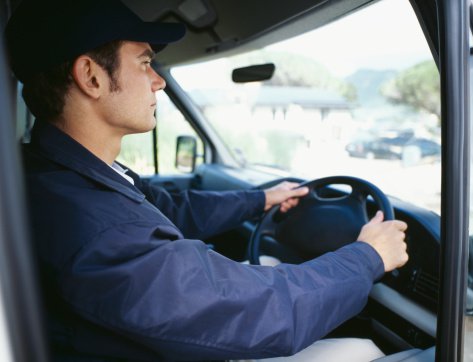
Truck drivers are one of the most important, yet unappreciated professionals in the US. The job isn’t easy – it’s full of risks and challenges. Truck drivers deliver about 70% of all freight in the U.S. — they provide life’s essentials. Almost 80% of US communities depend solely on the trucking industry for the delivery of goods. Without drivers, there would be no food at the supermarket, no medicine in the hospitals, and no fuel at the gas station.
7 Benefits of Centralized Transportation Management
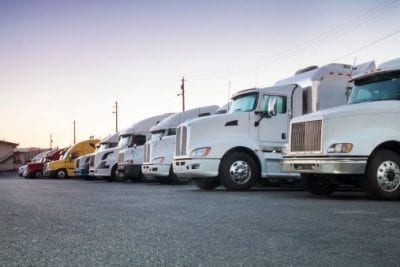
If your business is interested in increasing visibility, improving performance and reducing spend, then TMS technology is the tool you need. TMS software offers an assortment of benefits, including better management, simple monitoring, aggregated data, and stress-free integration. By improving freight management, scheduling, operations, and reporting, this technology provides superior customer service, flexibility and intelligence.
3PLs Drive Sustainable Supply Chain Solutions
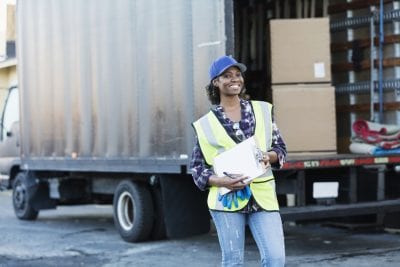
Environmentally-friendly business processes are good for the bottom line and the ecosystem. While most companies have stepped up to keep customers educated on their green initiatives, many have yet to expand those efforts throughout the supply chain. Using a 3PL for supply chain management can be very beneficial to companies.
Advantages of Combining Backhaul Freight
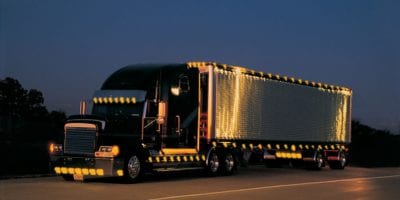
Shippers everywhere have faced limited capacity because of the driver shortage and shrinking numbers of trucks in the industry. These shippers must discover effective ways to handle transportation with limited resources. A shipper can learn how to be carrier-friendly or spend time searching for the cheapest freight rates, but they can also take advantage of continuous moves. Combining backhaul freight isn’t a new transportation strategy, and it proves to be cost-effective and time-saving.