A Simple System for Small Shippers to Automate Transportation Management
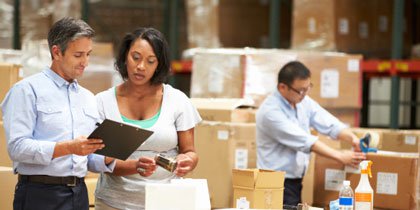
Do you still coordinate transportation operations manually? Shippers who operate this way don’t reach the best decisions and usually make costly administrative mistakes, sometimes without even knowing it. Automating transportation management provides numerous opportunities to save money and time while creating better service for customers.
PLS Recognized by Pittsburgh Business Times in List of Largest Private Companies
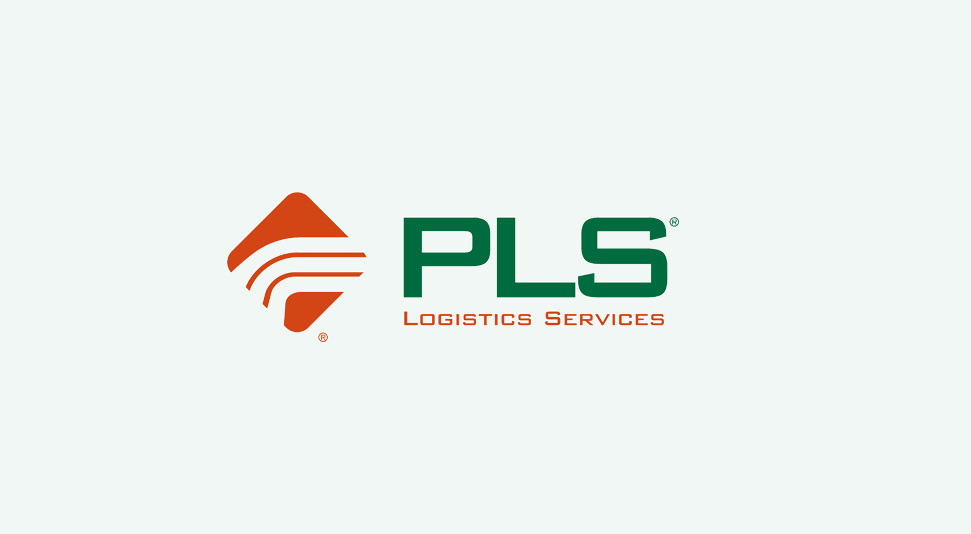
PLS Logistics Services (“PLS”), a leading provider of technology-enabled transportation management and freight brokerage services, was featured in the Pittsburgh Business Times’ 2015 List of the Largest Pittsburgh-area Private Companies. The annual list highlights privately owned area businesses with annual revenue above $20 million.
July Transportation News Round Up
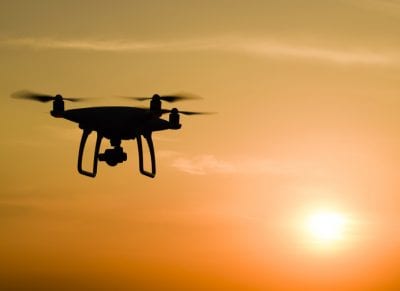
We’ve been keeping track of the various news stories affecting the transportation, supply chain and logistics industries. Here is a quick look at some of the most talked about topics:
Carriers – Reduce Emissions without Making Truck Changes
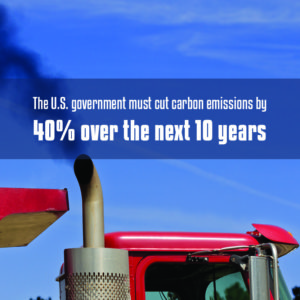
Over-the-road (OTR) freight carriers face pressure from shippers and customers who want impeccable service, and the government who wants advances on environmental performance. In March, President Obama made an executive order that mandates the U.S. government to cut carbon emissions by 40 percent over the next decade, setting an example for industries across the country.
Less Than Truckload Shipping: An Ultimate Guide
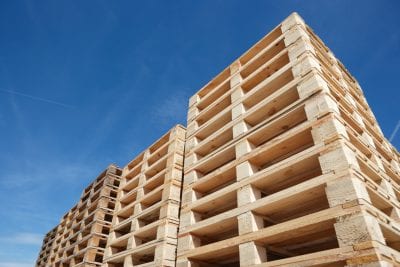
What is less than truckload freight shipping?
Less than truckload shipping is a transportation method where your freight doesn’t take the entire container space. Freight is combined into one trailer with multiple shipments. LTL shipment typically weighs between 151 and 20,000 pounds. When a freight shipment isn’t large enough to fit into a 48- or 53-foot trailer, a shipper’s best option is to use LTL.
Infographic: The Cost of LTL Shipping
Less than truckload (LTL) shipping doesn’t have to be complicated or expensive. In order to drive savings to your LTL transportation spend, it’s important to understand the factors that determine LTL pricing, including, minimum rates, freight classifications and accessorial fees. And, many carriers are increasing their LTL shipping rates because of fuel prices and tight capacity. Learn how you can avoid additional fees and ship your LTL freight effectively.
How Cross Border Shipping Can Benefit You
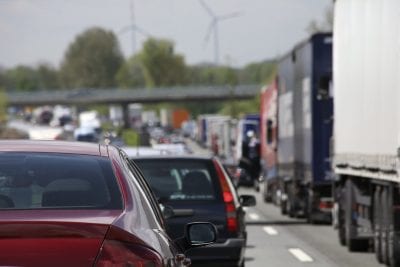
Cross border shipping requires knowledge, flexibility, and security. In North America, many companies have expanded or plan to expand their business operations throughout the continent. With cross border operations, there is an opportunity to reach new markets and increase profitability. According to the US Census, Canada is America’s largest trading partner and Mexico is America’s 3rd largest trading partner. cross border shipping
4 Benefits of SaaS TMS Software
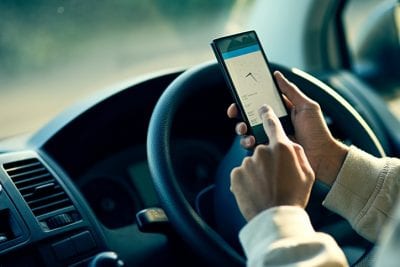
There are a variety of transportation management systems (TMS) software available, including premise, hosted and SaaS (Software as a Service) models. The SaaS model has become an industry preference.
What Is Intermodal Transportation & How Can It Benefit You?
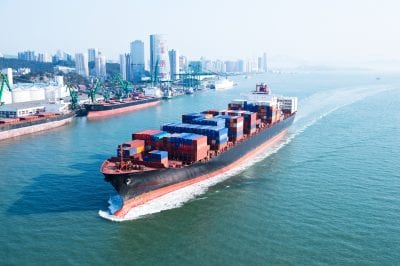
Intermodal freight transportation is a combination of two or more different shipping modes like a truck, rail, ship, or aircraft to move freight to the final destination. Also, in intermodal logistics and transportation, each carrier is responsible for a particular mode.
Final Rule for ESCs
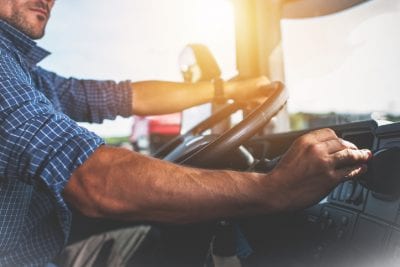
In early June, the National Highway Traffic Safety Administration (NHTSA) issued a rule requiring new heavy duty trucks to be equipped with electronic stability control (ESC) systems. In 2017, the rule will affect all trucks and buses exceeding 26,000 pounds in total weight. Electronic stability control systems are widely used in passenger vehicles and light trucks, and many heavy vehicle trucks have voluntarily chosen to use ESCs.