State of Rail Transportation: Rising Costs but Still Viable Option for Shippers
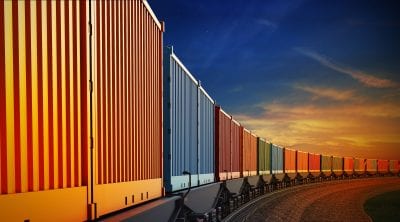
Rail transportation has historically been cheaper and slower than over-the-road (OTR) transportation. It’s a valuable service for raw materials, freight that is not time-sensitive or freight that is expensive to haul. As OTR costs rise, many shippers look for new opportunities to reduce overall transportation spend, and despite the current rise in rail costs, intermodal is a practical alternative.
Trending Transportation News: February 2016
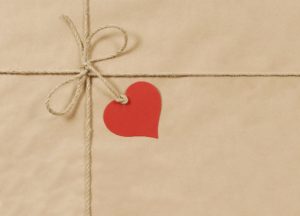
Non-Manufacturing Grows for 72nd Straight Month. The Institute for Supply Management (ISM) reported that non-manufacturing activity continues to point towards growth. ISM uses the NMI index to measure non-manufacturing growth and found the economic activity in the non-manufacturing sector continued to grow especially in finance/insurance, real estate/rental, agriculture, health care and public administration.
The Independent Steel Alliance and PLS Logistics Services Partner to Provide Independent Rebar
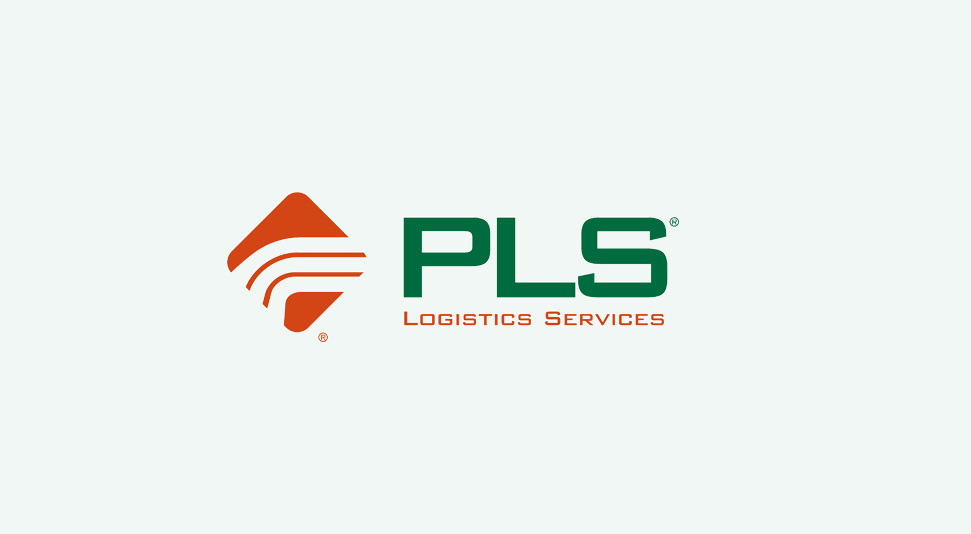
The Independent Steel Alliance (“ISA”) has signed a transportation partnership agreement with PLS Logistics Services (“PLS”), a leading logistics management services provider. This agreement will allow ISA’s purchasing members to receive freight transportation services at competitive rates while earning loyalty rebates in exchange for selecting PLS as their preferred carrier.
Resilience in Supply Chain Management: Best Practices
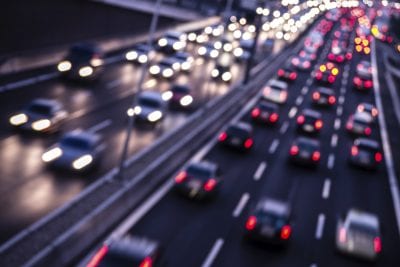
What is resilience in supply chain management?
Supply chains are diverse and complex, so are the potential risks that could disrupt them. A good supply chain management strategy invests in resilience. Resilience refers to the time it takes supply chains to predict and avoid risk, as well as respond and recover from costly disruptions. how to supply chain management strategy75% of companies experience at least one major supply chain disruption a year.
The Remarkable Impact of Processing Big Data in Transportation
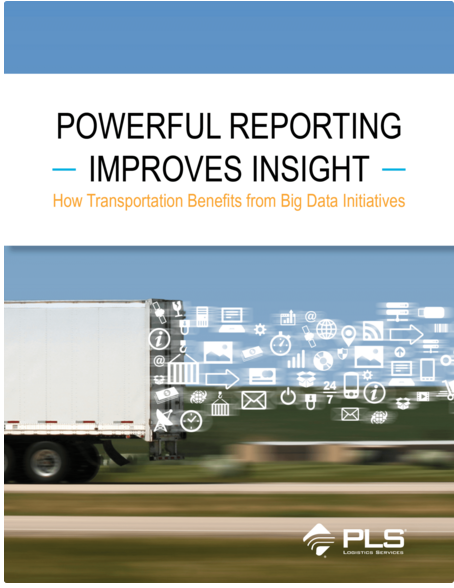
Only 23% of companies have a big data strategy, which isn’t surprising, considering there’s an estimated 2.5 quintillion bytes of data created each day. It’s impossible to analyze it all, but leveraging big data in transportation and logistics can enhance operations and elevate the bottom line.
What is ITS and How Will it Help America’s Infrastructure?

Automated_Trucks.jpgTraffic and population growth create demand for new roads, but most regions don’t have space or money to build new infrastructure. Today’s concerns over infrastructure, traffic congestion, energy use, and safety are being addressed by new transportation-focused technology.
Market Update: Industrial Distributors Have Serious Service Issues
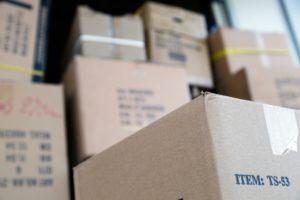
It’s a difficult economy for industrial distributors. Industrial demand is down – in Q4 of 2015, manufacturing orders were down 20% YoY. Amazon’s low prices and convenience make it difficult to compete. The drop in oil prices, cheap imports, and the strong U.S. dollar all affect manufacturing output, which leads to lower revenues for distributors.
PLS Logistics Services Continues Expansion, Opens Office in Las Vegas
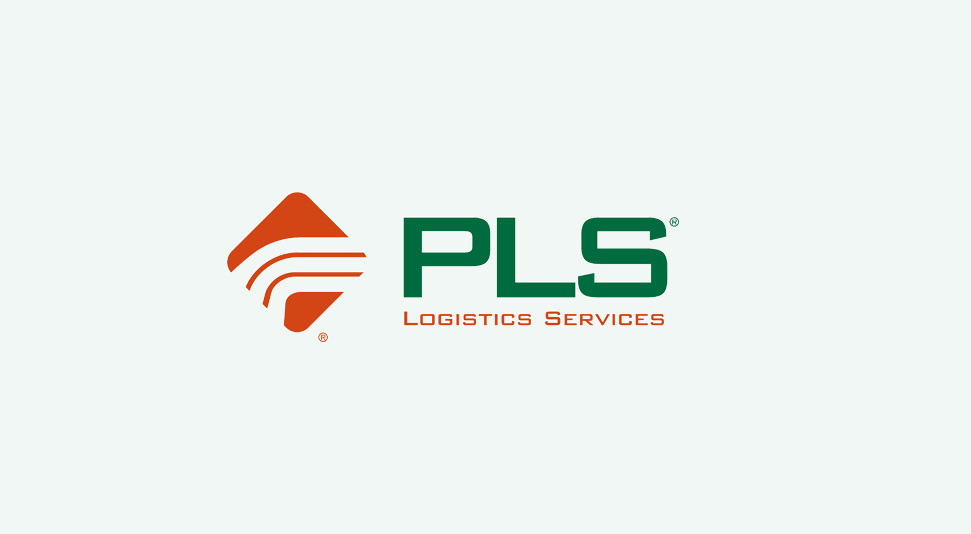
The office opened February 15, 2016, with an initial team of 20 employees and expects to hire 200 additional employees in 2016 from the Las Vegas area. The office is located in the Bank of America Plaza at 300 South 4th Street, Suite 600, Las Vegas, Nevada.
E-Commerce Changes Traditional Retail Shipping Strategies
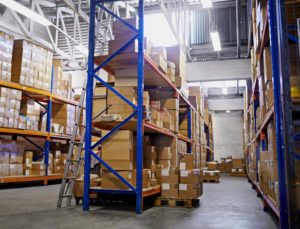
Customer demand and connectivity are high, and retailers are struggling to keep up with the competitive omnichannel environment. Supply chains are shifting in order to accommodate the rapidly changing landscape for the way people buy and the way goods are moved.
Tips for Delivering Temperature-Sensitive Goods
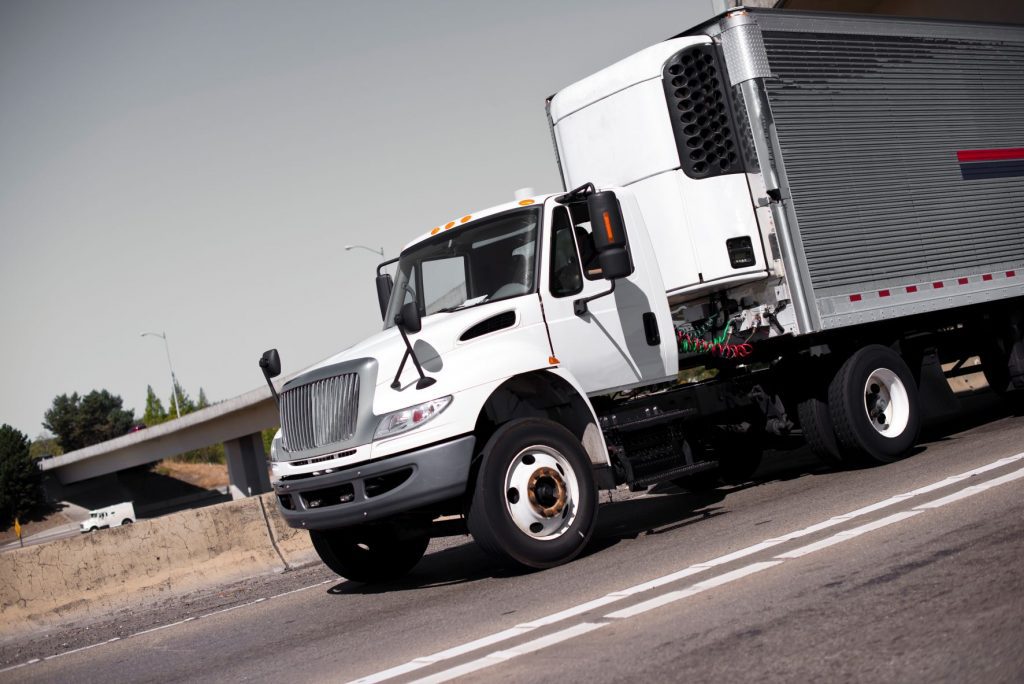
Shippers are able to manage the challenge of transporting temperature-sensitive goods; from farm produce to fresh flowers, thanks to refrigerated shipping trailers. Refrigerated trailers can remove or pump heat or create a cool environment for products to be transported in. Refrigerated trailers are designed to maintain the pre-cooled cargo temperature. Maintaining the temperature in a refrigerated shipping trailer, or reefer, is necessary in order to not compromise the product. Failing to maintain the proper shipment temperature can result in serious consequences like wasted or damaged products and sunken costs.