Trending Transportation News: December 2015
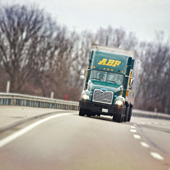
Here’s a recap of transportation news stories throughout the month: Werner Increases Driver Pay. Effective January 1, Werner Enterprises Inc. is increasing pay for almost 1500 drivers. The drivers hadn’t had a pay increase since August 2014. President and COO, Derek Leathers said, “Pay increases are one piece of our multi-faceted approach to attract and retain the best in the industry and make Werner the employee of choice.” Read more: Drivers Enjoy Pay Increases, Shippers Pick up the Tab
A Look Back at 2015 and Preparing for Disruption in the Trucking Industry
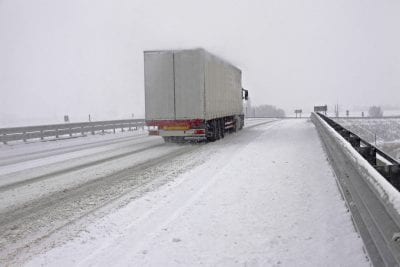
The transportation industry, specifically the trucking sector, is at a crossroads. Threatening conditions loom at a time when several technologies are positioned to disrupt traditional operational processes. It is up to carriers to plan ahead for the future.
Industry Expectations: 2015
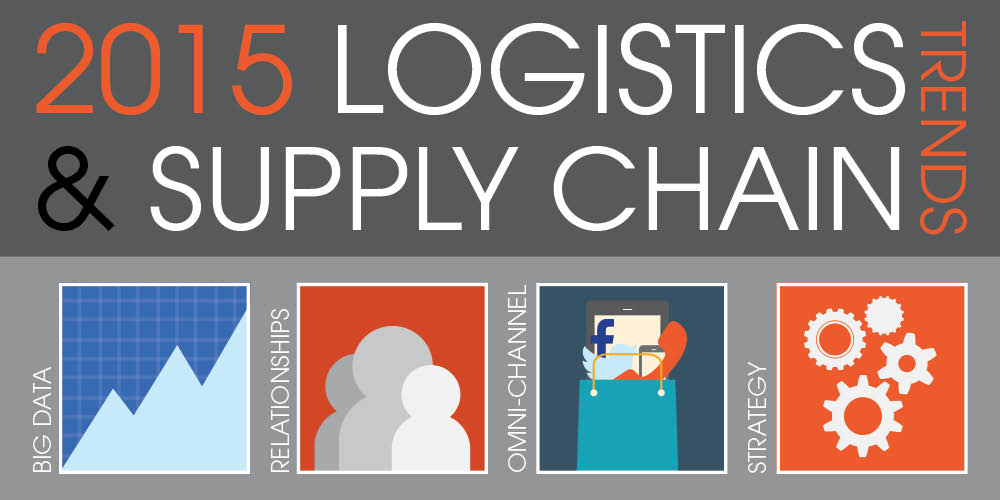
The New Year is quickly approaching, which means new challenges and opportunities can be anticipated; specifically in the supply chain and logistics industry.
Why Warehouse Technology is the First Step in Fast Shipping
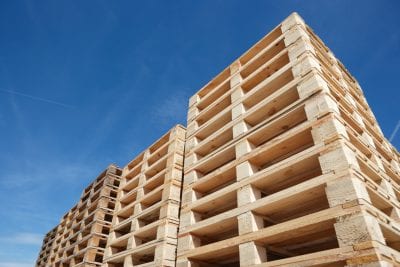
Companies implement supply chain management (SCM) strategies in order to meet customer expectations like fast delivery. Delivery time is the sum of fulfillment time and transport time. Companies are emphasizing the importance of fast fulfillment in order to reduce overall delivery time. Creating an SCM strategy includes aspects of logistics management and demand planning that work in tandem with a transportation strategy. It is a crucial step in reducing freight costs.
Market Update: 2016 – 2017 Trucking Regulations May Aggravate Economic Trends
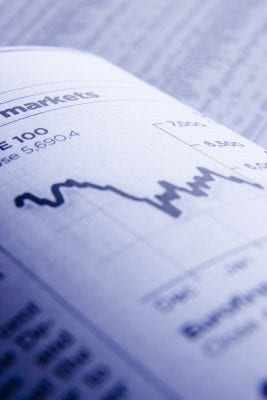
The over-the-road (OTR) trucking industry faces numerous regulations that are controversial within the industry. Due to the current state of the economy and the crucial turning point, it is at, these regulations have the potential to worsen the capacity crisis, increase transportation rates and harm carrier productivity at a time when carriers expect financial difficulty.
How Retailers Overcome Challenges of Seasonal Demand
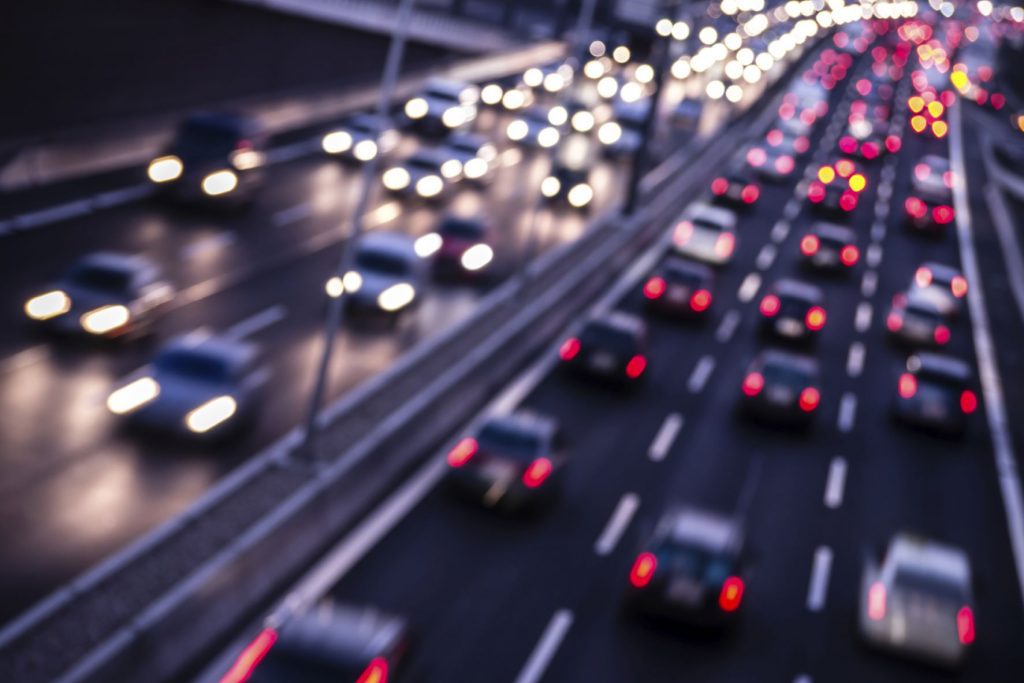
The biggest shopping weekend of the year is right around the corner, and retailers have been planning for the increase in sales for months. Most retailers have adopted to the omni-channel environment, merging numerous shopping channels for the convenience of the customer. Modern shoppers avoid the long lines and huge crowds associated with Black Friday to buy from online vendors who offer the same markdowns, plus free shipping and various return options. ShippingDisruption.jpg
Transportation Management Done Right: 3 Examples to Learn From
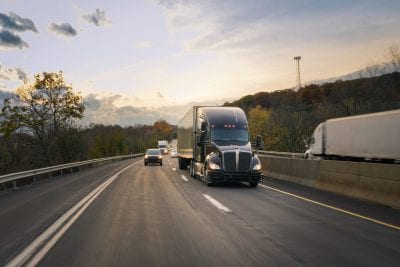
There are an array of challenges when it comes to successfully applying an outsourced transportation management strategy. Companies want to make freight moves as efficient as possible, which means centralized systems, qualified carriers, managed schedules and visibility. Realizing opportunities for transportation efficiency starts with identifying challenges. Below, we examine different challenges from 3 companies and how PLS solutions created and maintain notable results.
5 Key Components of Good Transportation Management
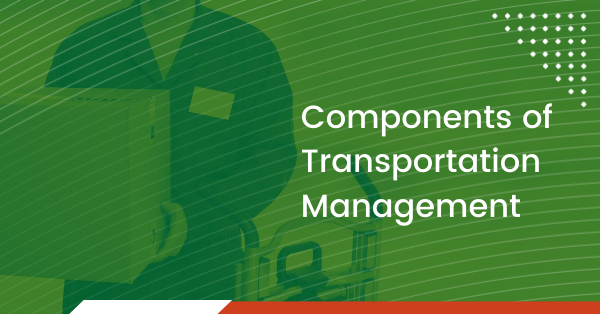
Investing in a robust transportation management strategy can significantly improve your overall business by decreasing costs and satisfying customers.
Understanding Risk for Midstream Transport
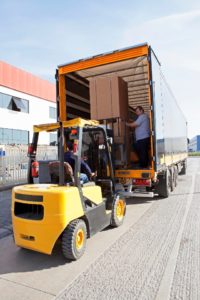
Moving over dimensional machinery, hazardous products, and required equipment to natural gas processing plants and compressor stations on- or off-highway can present safety problems. Every shipment is a large risk for midstream oil companies because the penalty for an accident or non-compliance is enormous.
PLS Logistics Services Continues Expansion, Opens Office in San Antonio
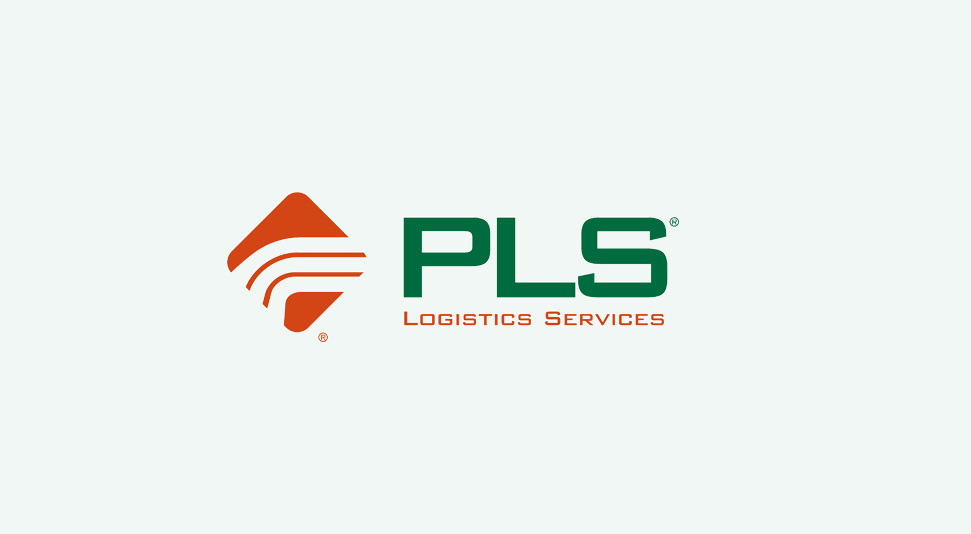
The office opened December 14, 2015 with an initial team of 10 employees and 40 new hires in 2016 from the San Antonio area. The office is located in the Weston Centre at 112 East Pecan Street, 6th Floor, San Antonio, Texas and is expected to create more than 200 jobs in the region over the next three years.