Trending Transportation News: July 2016
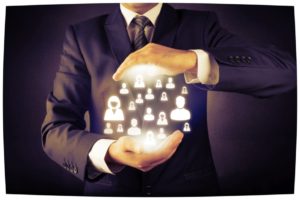
FedEx Delivers to Cuba. FedEx became the first American freight carrier with rights to deliver freight to Cuba. FedEx says they will begin service on January 15, 2017. Their rights extend to July 15, 2018.
More Connected Devices Creating Supply Chain Vulnerabilities
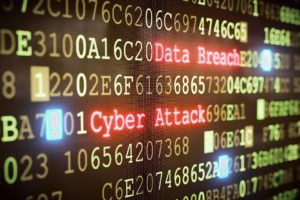
Cyber-attacks are an increasing threat in the transportation and logistics industry. Transportation and logistics are integral to the world’s economy, and therefore, a valued target for hackers.
6 Common Supply Chain Disasters You Can Easily Avoid
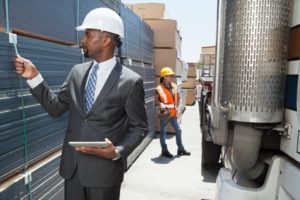
Supply chain mistakes are costly. The smallest error is amplified due to the sheer size of a supply chain. It is crucial for companies to maintain best practices in supply chain management.
CSA Scores to Make Early Comeback?
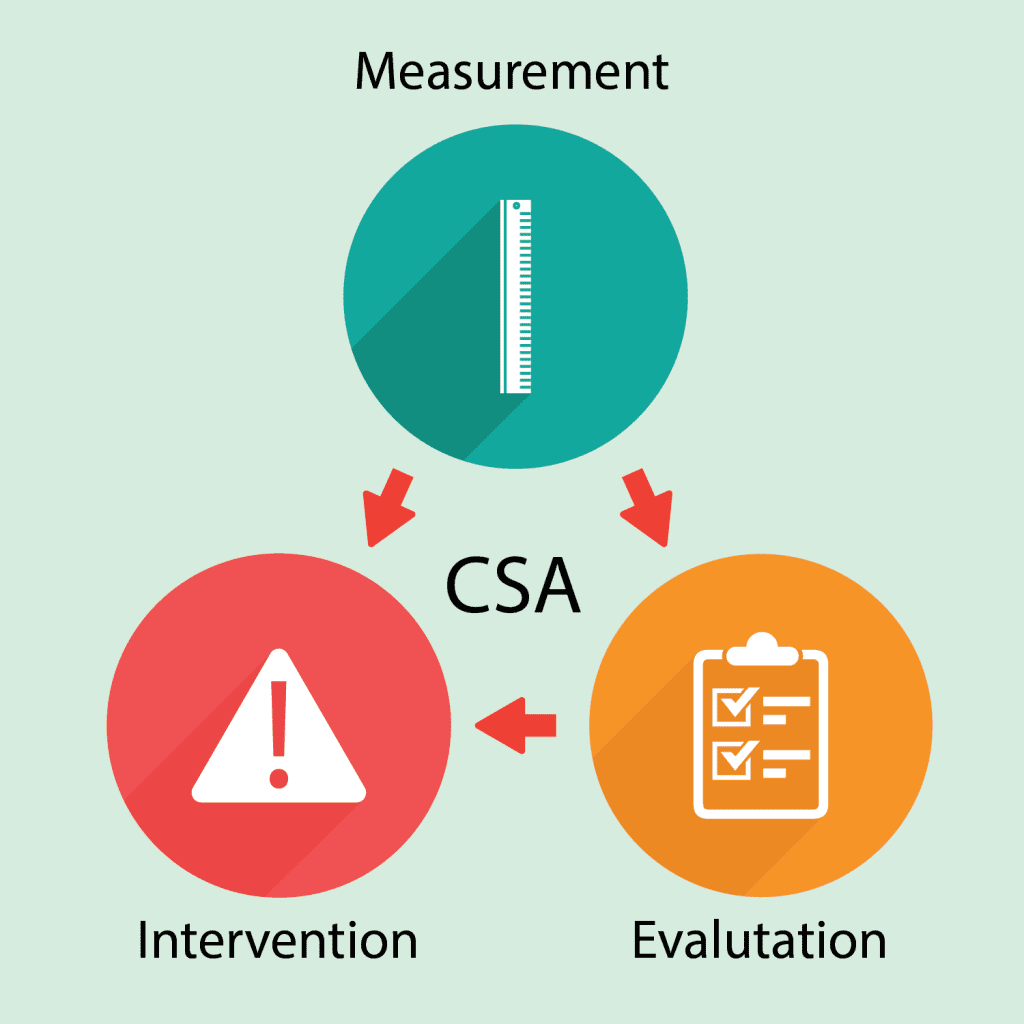
In 2015, the FAST Act required FMCSA to remove CSA (Compliance, Safety and Accountability) information from public view. It also mandated that FMCSA repair the CSA program so that scores can be used as a consistent, reliable safety measure.
2 Simple Reasons 3PLs Have Remained Extremely Popular
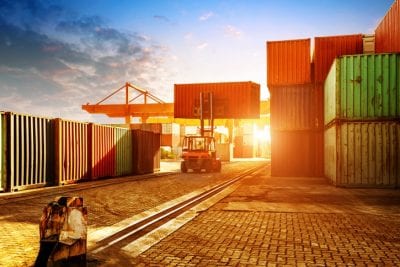
Despite the negative connotations of the terms ‘broker’ and ‘outsourced’, third-party logistics companies have gained popularity and are employed by nearly every industry in the U.S. How did this happen?
Competing for Customers? Improve the Last Mile
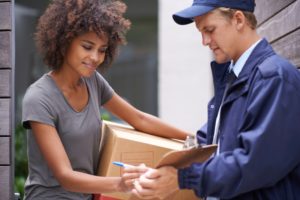
Last mile logistics refers to the movement of goods from a warehouse or distribution center to its final destination. To create customer loyalty, the last leg of transportation needs to be flawless.
PLS Logistics Contributes to the Blue Jeans Go Green™ Recycling Program
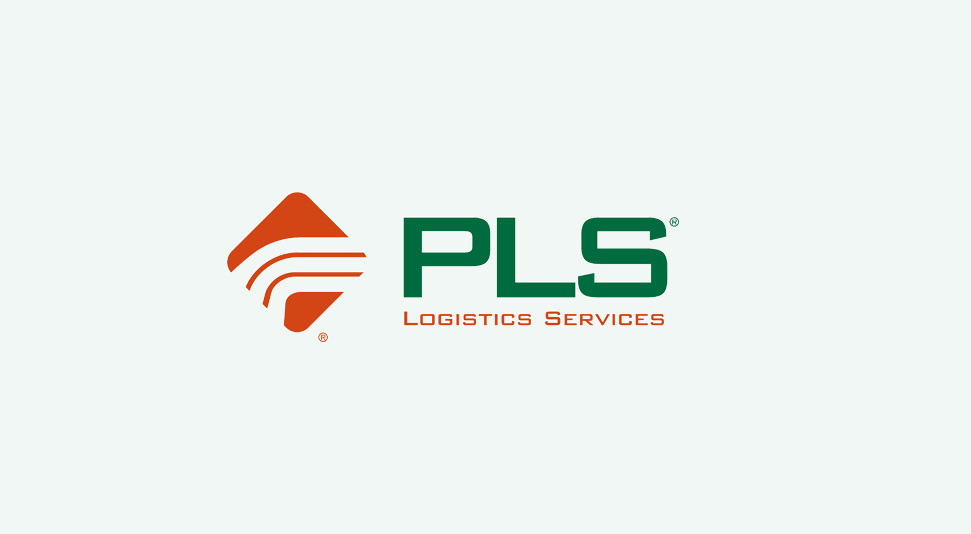
Employees recycled their old blue jeans, jackets, shorts and skirts, which will be turned into natural cotton fiber insulation. PLS collected 100 pairs of blue jeans over two weeks.
Why Right Now Is the Perfect Time to Invest In a TMS
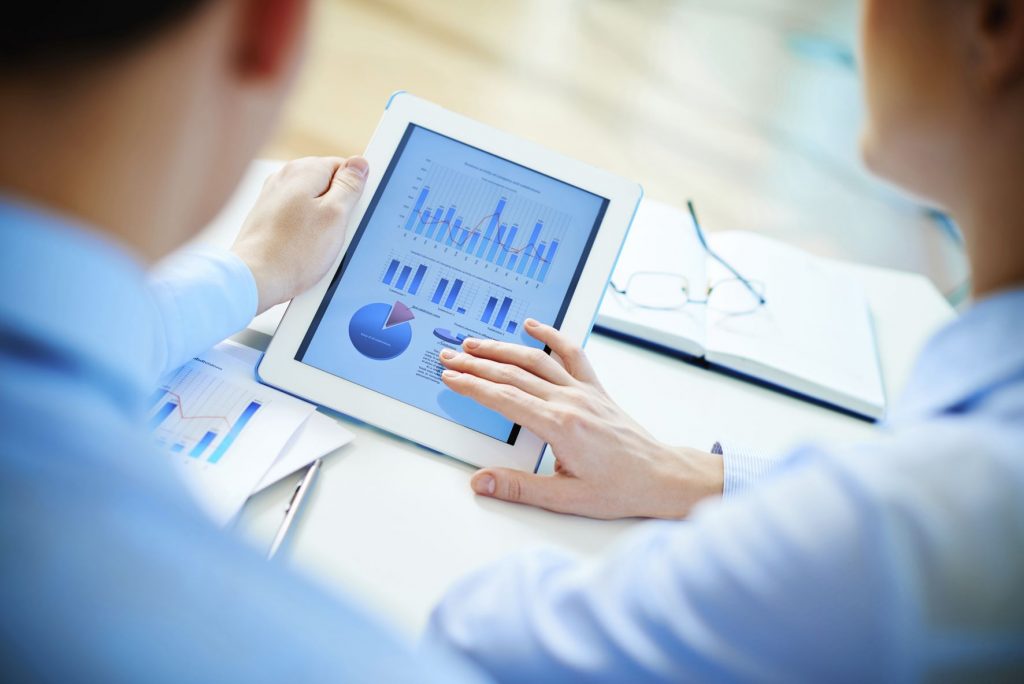
Despite the rapid evolution of today’s supply chain and the proven cost-saving ability of a transportation management system (TMS), few shippers are using TMS software. In fact, only around 35% of shippers have a TMS.
Panama Canal Expansion: Everything You Need to Know
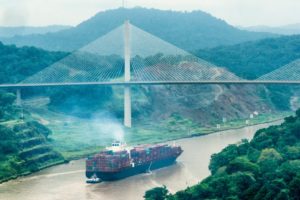
History of the Panama Canal During the 1800s, businessmen didn’t have an efficient or quick way to ship goods between the Atlantic and Pacific coasts. The British proposed a canal through Nicaragua that was never built and the French attempted to build a canal through Panama but evacuated the project due to fatal diseases. Despite the unsuccessful attempts, Americans were undeterred. In 1914, the United States began to build a canal in Panama.
PLS Logistics Services Recognized as a Great Supply Chain Partner in Annual Poll
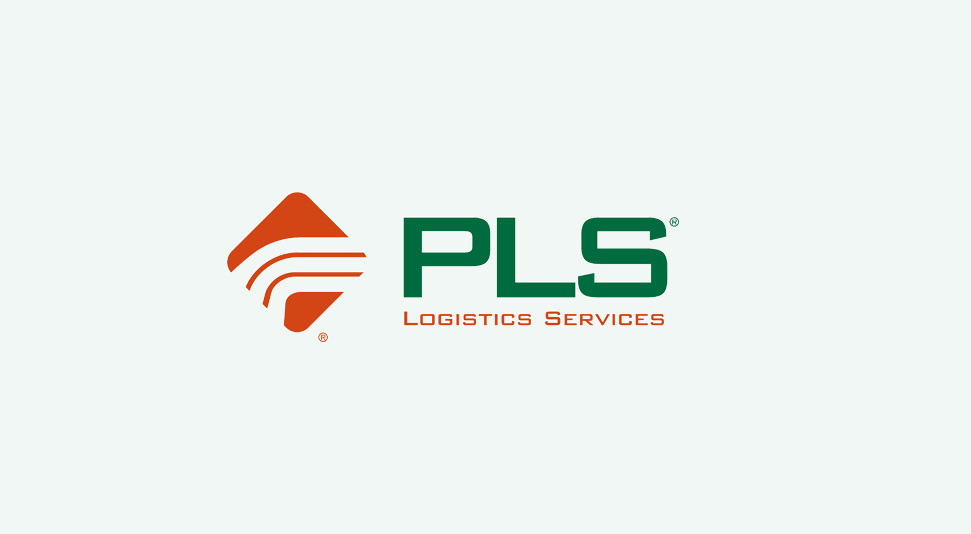
PLS IS NAMED ON SUPPLYCHAINBRAIN’S 2016 LIST OF 100 GREAT SUPPLY CHAIN PARTNERS