Trending Transportation News: April 2016
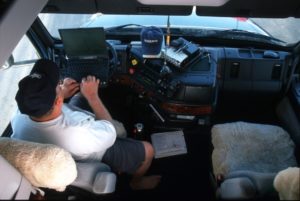
2014 Traffic Costs Industry $49.6 Billion. US highway traffic congestion added billions of dollars in operational costs for the trucking industry. More than a dozen states experienced congestion costs of more than $1 billion. 89% of the congestion happened on 12% of roads. The ATRI’s analysis showed that trucks were delayed more than 728 million hours.
3 Ways Supply Chain Cost Analysis Help Your Business
Cost_TMS_Report.pngAre you overpaying for inbound shipments? Should you switch from LTL to truckload shipments? Are your supply chain and dock loading processes proficient?
Climate Change Disruptions in Transportation
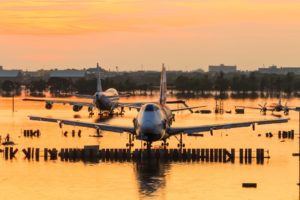
Disruptions are Difficult to Manage
Businesses are woefully unprepared for disasters and disruptions in their supply chain. In fact, two-thirds of employees say their businesses have not reassessed safety and crisis plans since the last time they faced a natural disaster.
How to Improve Loading Dock Processes
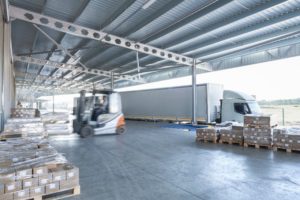
The loading dock is the access point for shipping and receiving. Well-designed loading dock procedures minimize delays, reduce damage to cargo and optimize productivity.
PLS Logistics Services Named to Top 25 Freight Brokerage Firms List 2016
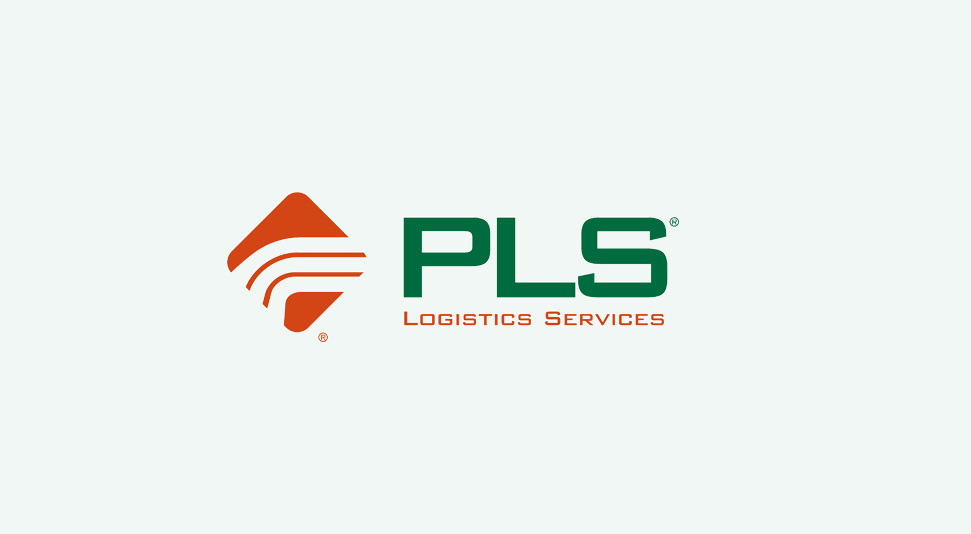
The annual list ranks freight brokerage firms based on net revenue. The Top Brokerage Firm list is part of Transport Topics’ Logistics 50, a yearly review of the largest logistics companies.
How This Company Grew Supply Chain Visibility With a 3PL Partnership
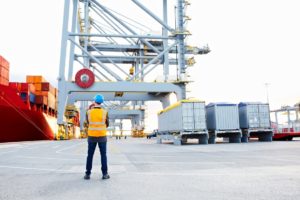
3pl for supply chain visibilityA common transportation challenge of B2B and B2C businesses is lack of supply chain visibility. Without visibility, deliveries are slower, so inventory management suffers and it’s more difficult to manage risk. These challenges appear because of additional costs and unhappy customers. Also, companies can use 3PL for supply chain visibility.
The Building Blocks of Transportation Visibility
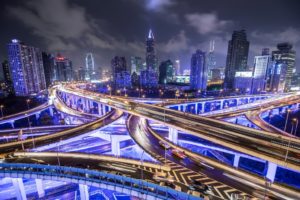
Many businesses want to leverage big data in supply chain initiatives to drive efficiency, cost savings and unparalleled operational visibility. In order to do this, however, a business must have an enterprise-wide infrastructure for information gathering. Only 35% of organizations use a transportation management system (TMS), meaning most companies do not have much visibility into shipping processes, but more importantly, don’t have access to data that’s part of the end to end supply chain insight that’s necessary for big data initiatives.
5 Ways to Increase Shipping Speed Without Using Expedited Services
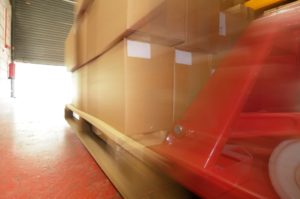
You need to send your freight quickly but don’t want to pay for expedited freight – it’s a dilemma all shippers face. Many companies rely on expedited shipping, but, with some simple operational changes, you can contain transportation costs and meet service expectations at the same time.
Shocking Statistics about Cargo Theft
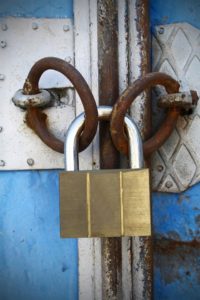
A new report finds that the number of recorded cargo thefts and the average value of the freight attacks declined in 2015. But, regardless of this data, cargo theft is a real problem. Cargo’s value continues to increase, and thieves are sophisticated. Cargo theft is estimated to cost shippers and trucking companies at least $30 billion a year in the US, according to the FBI.
Ocean Capacity: Bad News for Commodities Shipping
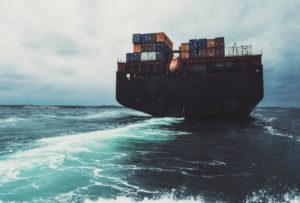
The Chinese economy drives demand for freight on the seas, and its economy’s existing weakness is weighing on the global shipping industry. Ocean shipping is necessary to the global economy, but shippers are experiencing somewhat of a crisis: low demand and surplus shipping vessels for hire. China’s slow economy is reducing demand for commodities like coal and iron ore, which affects dry bulk ocean transport.