March Transportation News Round Up
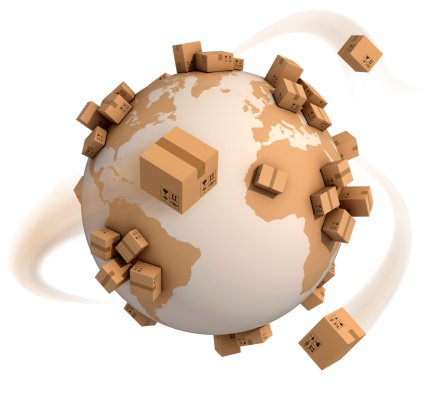
We’ve rounded up the top 5 news stories from March that are impacting the transportation industry. logistics-industry-professional
Delays from the Snowy Winter: More than 70% of the nation’s roads are in snowy regions. Winter weather is finally fading, but the snow storms caused major shipping delays.
The EPAs Green Transportation Initiative
The SmartWay Transport Partnership, launched in 2004, is an innovative green transportation initiative between the U.S. Environmental Protection Agency (EPA) and the freight industry, designed to reduce greenhouse gases, non-renewable resource consumption, and transportation costs.
The Secret to Meet Demand
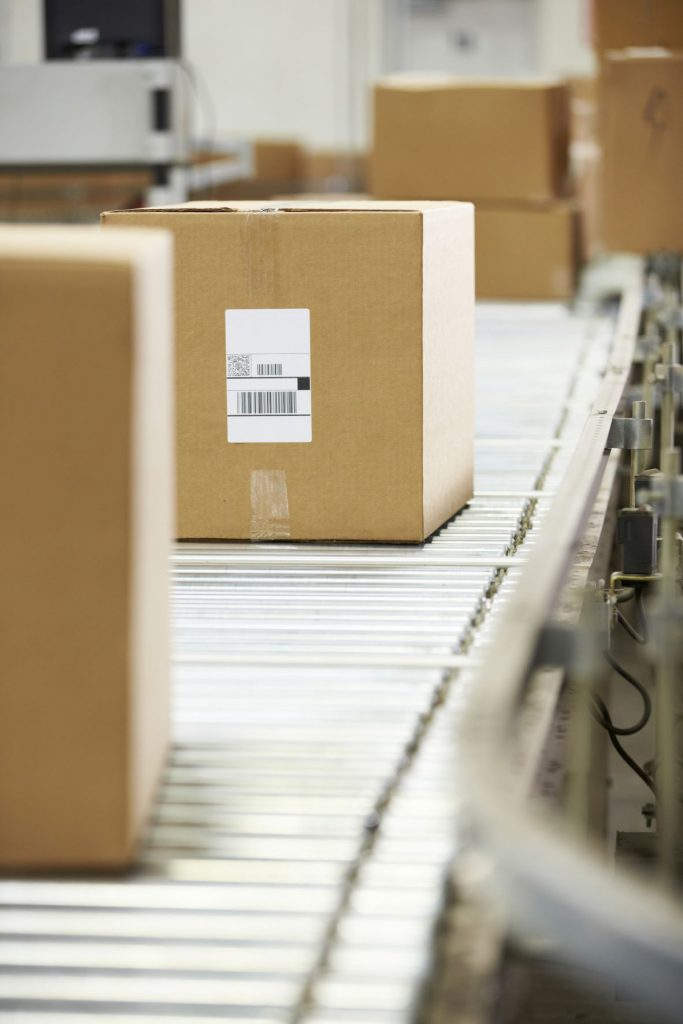
AutomationSeasonality affects almost all businesses. Supply production is rarely affected by seasonal factors, however, demand for products is subject to the season’s fluctuation. Seasonality can be explained by philosophies, customs, weather and/or holidays.
Why You Need to Consider Expedited Shipping
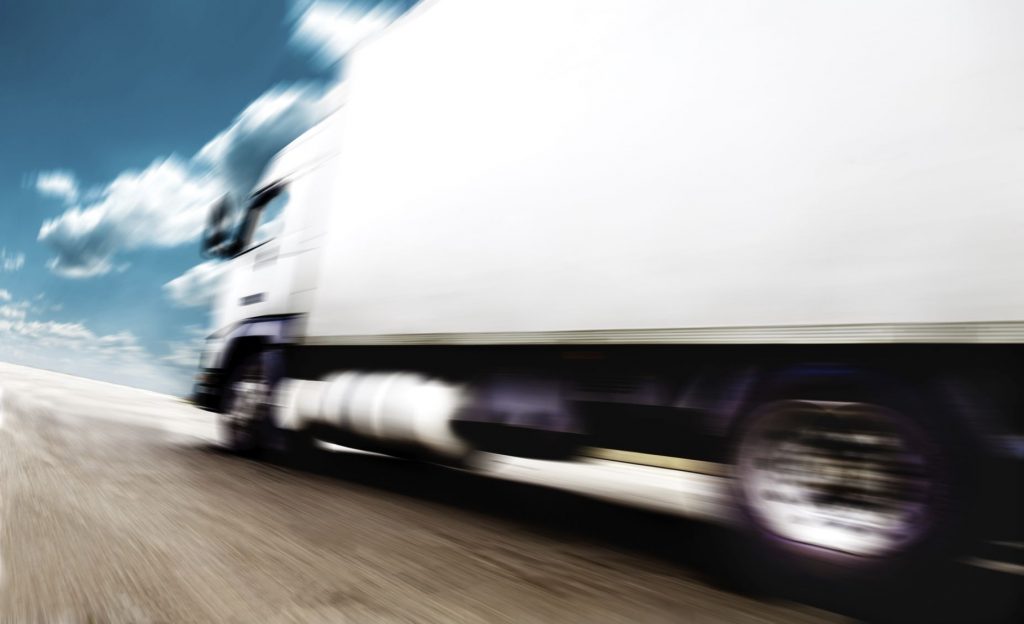
What is expedited shipping?
Expedited shipping is the process of transferring freight faster than normal. Whether your freight is perishable or you’re on a time schedule to meet customer expectations, expedited service has the ability to guarantee delivery requirements.
5 Best Practices for Supply Chain Management Strategies
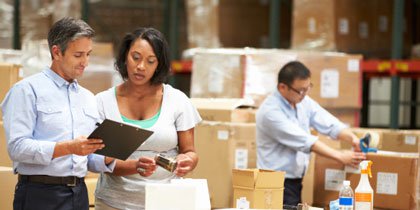
Implementing an operative supply chain management strategy is essential to efficiently transfer products throughout your supply chain.
Managing Produce Shipments
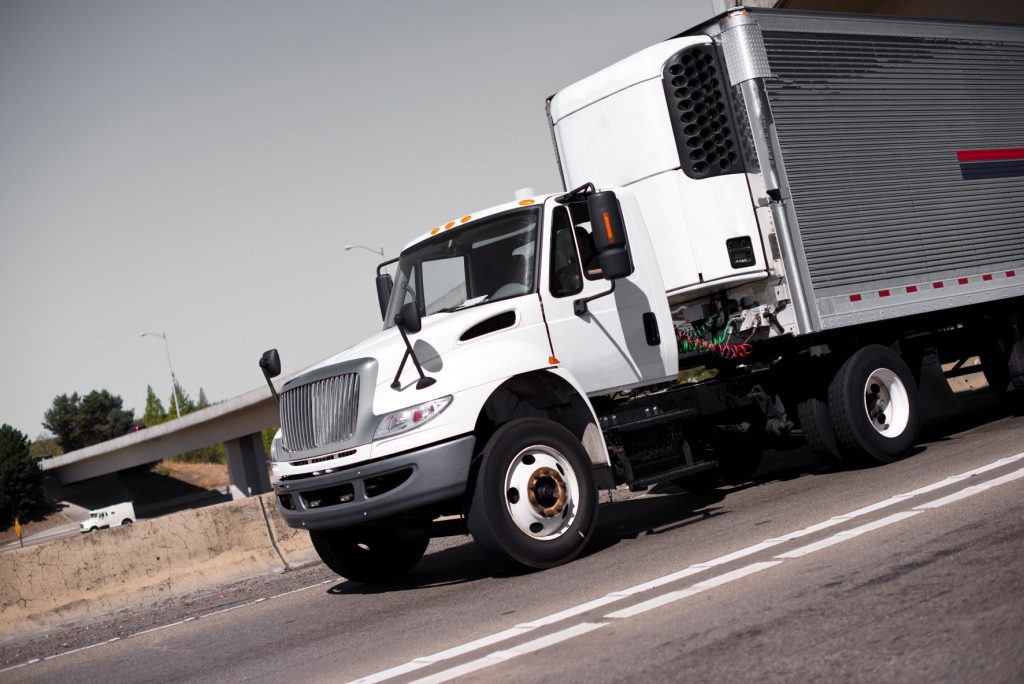
What is refrigerated freight transportation?
Refrigerated freight is a transportation method used when the cargo being shipped must be controlled by a defined temperature. Produce is one of the many products transported by a refrigerated trailer. Refrigerated, or reefer, transport should account for a trailer’s operating characteristics, the load temperature and the transit temperature of the product.
PLS Logistics Services Hires Dave Mabon as Chief Operating Officer
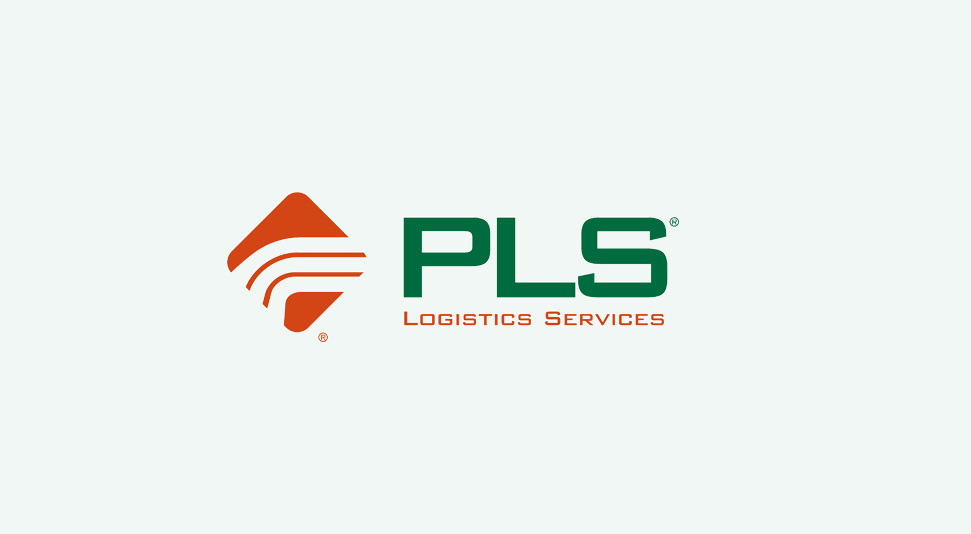
Mr. Mabon most recently served in a variety of executive leadership positions with GENCO, a North American logistics provider. Previously, he directed sales and marketing for Kuehne + Nagel’s Contract Logistics business unit and served on their International Logistics Steering Committee. Mr. Mabon started his logistics career with APL.
Create Visibility through Reporting
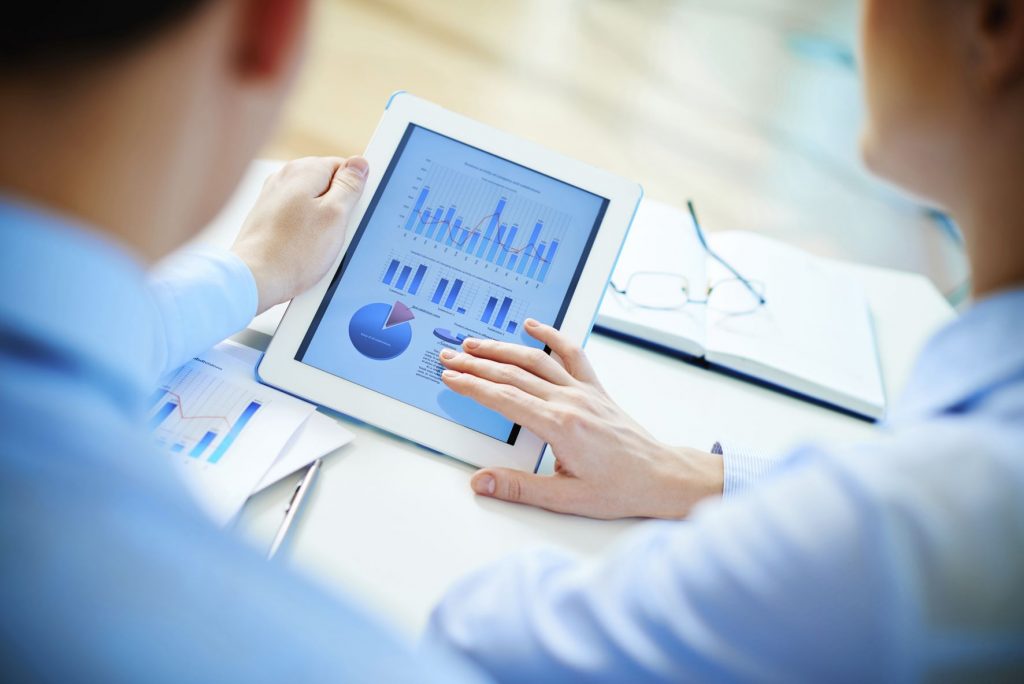
Customized reporting capabilities provide supply chain visibility and enable process improvements. If you are working with a 3PL, access to clear, concise, timely and customizable reports should be an essential element of your partnership. Shippers should have the ability to filter, sort and manage their data in real time to make decisions and improvements.
Why Fuel Surcharges Don’t Match Cheap Gas Prices
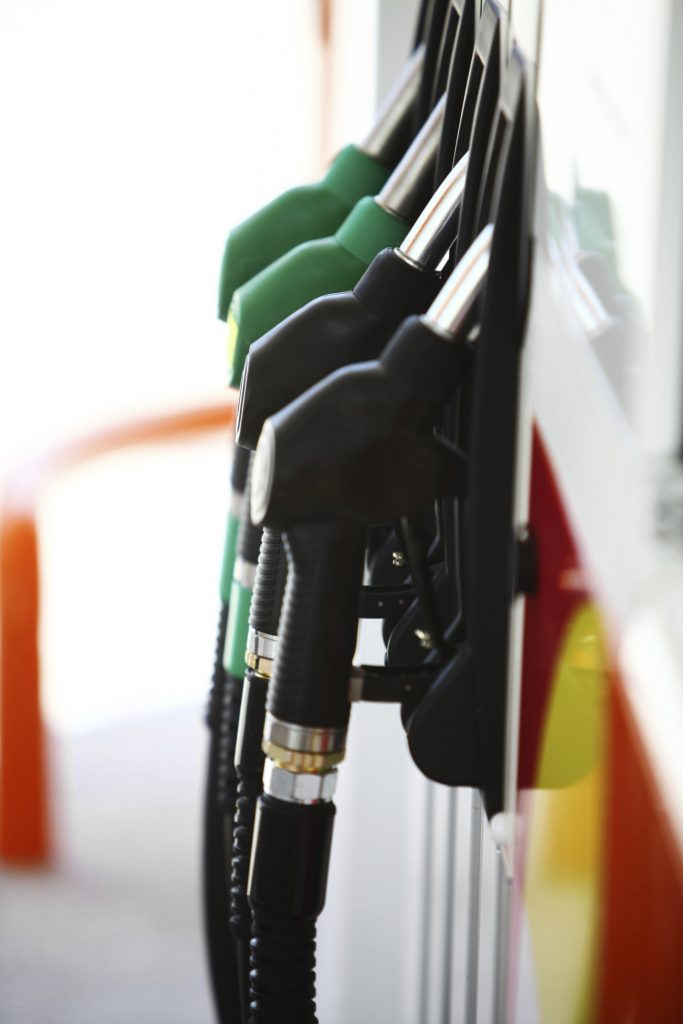
The cost of oil has been falling and so have gas prices; reaching lows that haven’t been seen in over a decade. Even though diesel fuel hasn’t seen price drops like regular gasoline, carriers are still seeing a difference in their bottom line. However, they are not profiting as you would expect.